The ELGi Foundry
We make air compressors and the metal castings for it as well.
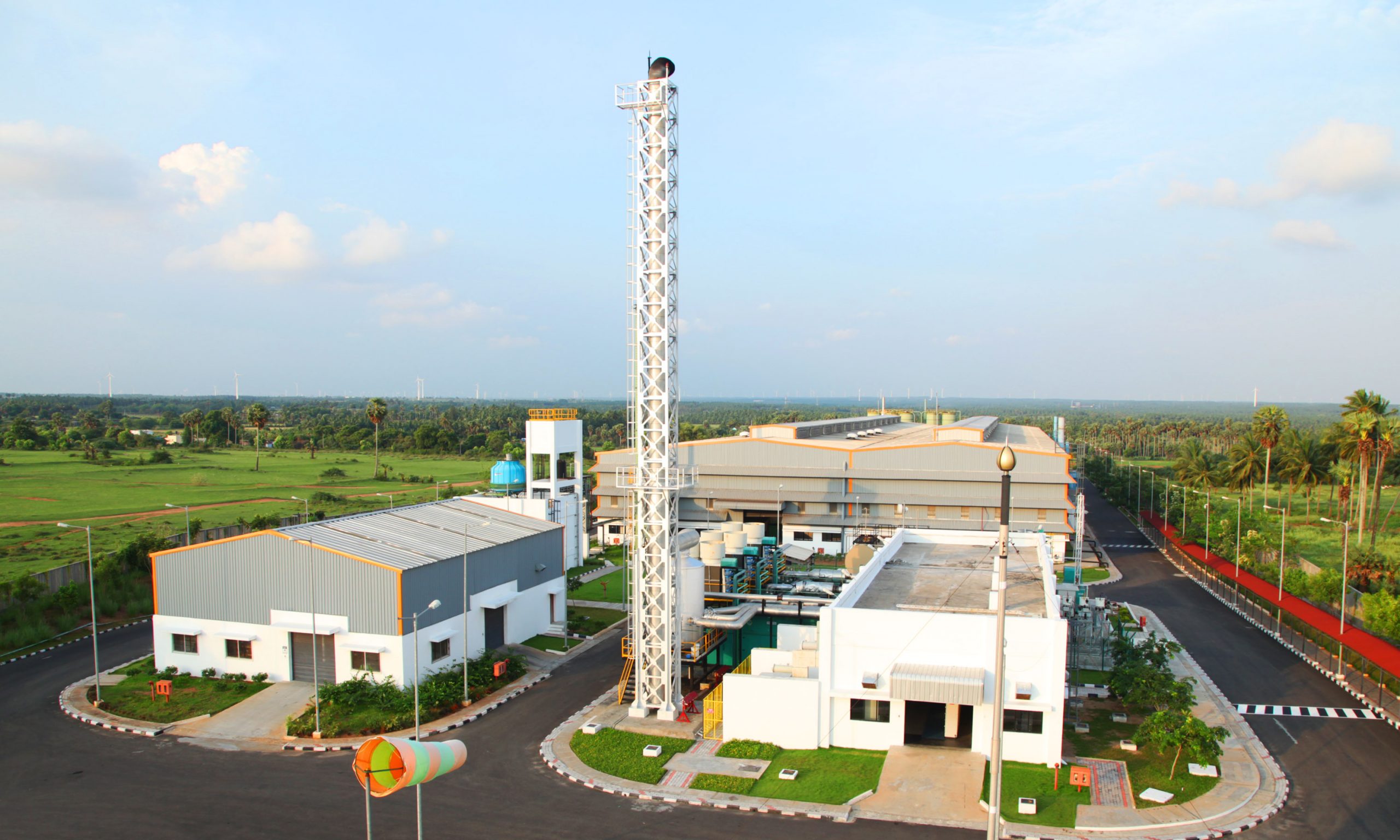
The Indian foundry sector is the third largest in the world after China and the US. Foundries in India operate either as feeder units for manufacturers such as automobile or heavy equipment companies or as captives that produce metal castings for their own products. They work on a variety of metals such as grey iron, ductile iron, steel and aluminium alloys. India produces 11-12 million tonnes of castings a year.
Foundries occupy pride of place in Coimbatore’s identity as an industrial town. With over 500 units, it is the largest cluster of foundries in the country. It is also going to play a big part in fulfilling the country’s Make in India dream. This manufacturing hotspot is expected to see increased activity in the next couple of years, with a projected annual growth of 13-14 percent as against 5-7 percent in the past few years.
ELGi set up a foundry in 2013 to manufacture its own special castings for its air compressors. Among other applications, the castings manufactured at the foundry are used to make ELGi’s proprietary eta-V airends. ELGi produces close to 14,000 airends a year that power its wide range of compressors.
ELGi is perhaps the only company in the world with a foundry that makes metal castings for its own airends. The custom-designed castings follow international quality benchmarks for thermal distortion and deflection. The foundry fits into the company’s vision of becoming a world leader with its range of distinctive products that caters to a global customer base.
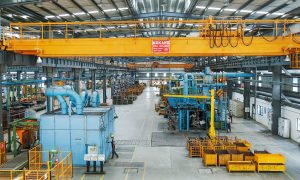
“By building our own captive foundry, we have made huge investments. But the investment has paid off since it has given us control over quality and production cost. This in turn has given us the confidence to assure our customers of product excellence,” says Managing Director, Elgi Equipments, Dr Jairam Varadaraj.
Located on the outskirts of Coimbatore, the-state-of-the-art foundry is ISO-9001 and PED certified. The 100,000 sq ft factory is built on a sprawling 9.6 acres plot and has an installed capacity of 9,000 metric tonnes of grey and SG cast iron per annum. The foundry uses an automated fast-loop Furan moulding process that is capable of manufacturing castings of 32 kg to 3.2 tonnes, with tolerances that conform to standards such as ISO 8062.

It employs Furan and Amine Cold Box techniques for the core making. Melting is done in a dual-track, induction furnace of two-tonne capacity with a melt manager of 1,500 KW. The mmetallurgical and mechanical properties of the output from the melt manager conform to national and international standards.
To ensure that the foundry meets global standards, ELGi has acquired next-generation equipment from world leaders like IMF, Italy, and DISA. Meticulous planning has gone into the foundry’s layout to ensure process efficiency. The company has brought in automation to improve process quality and increase production.
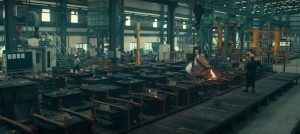
Process automation
The main process equipment is divided into different work stations, each controlled by a programmable logic controller (PLC) with user-friendly displays at the control panels for ease of operations. The PLC panels are connected to a supervisory control and data acquisition (SCADA) system that provides data to service providers such as IMF to improve operations or plan plant expansion in the future. SCADA also ensures accuracy of process parameters for example controlling sand filling.
Process automation at the foundry is aimed at reducing human intervention with a view to eliminating errors and variations, thus ensuring reliability. For example, automatic mould stripping and online baking of moulds ensure repeatability and accuracy in dimensions each time.
Technical talent
ELGi employs technicians and operators trained in the foundry department of premium technical institutes. They are tested on both theoretical knowledge and practical skills before being absorbed in the foundry.
Pollution control
ELGi has taken various steps to ensure that its employees work in a clean and healthy factory and that the operations have minimal impact on the environment. Some of the measures implemented are:
1. Mechanical and thermal reclamation units that recover and recycle 96 percent of the sand being used
2. Collection of dust generated including fine sand through custom-made equipment and converted into solid bricks
3. Installation of dust collectors, filters and wet scrubbers across the factory
4. Development of one-third of the factory site into a green belt with trees and landscaped gardens
5. A comprehensive solid waste management designed to minimise the amount of solid waste from the foundry
In recognition of these efforts, the Institute of Indian Foundrymen, Coimbatore chapter, was awarded ELGi foundry the Green Foundry Award in 2016
Employee well-being
Working at a foundry can be taxing on the mind and body. ELGi has taken several steps to create a conducive work environment for its employees. Some of the some of the processes we have in place are:
1. Shake-out machines enclosed within a sound-proof chamber to reduce noise levels from 100 decibels to less than 75
2. Extensive network of dust extractors, wet scrubbers and rooftop fans that ensure a dust-free and fume-free environment in areas where melting, core shop, fettling and primer coating operations take place
3. Installation of booths with dust extraction systems in fettling chambers
4. Feeding heavy metallic charge materials to the furnace through vibrators and magnetic cranes to suck in metallic dust particles
5. Use of clean LPG fuel for heating to keep environmental pollution in check
6. Automatic closing and stripping machines to ensure reduced work fatigue
“Sustainability is extremely important to us. We have taken care to build a foundry that helps us manufacture products of a superior quality without compromising on the environment and the well-being of those making those products,” says Dr Varadaraj.