Compressed Air In Thermal Power Plants
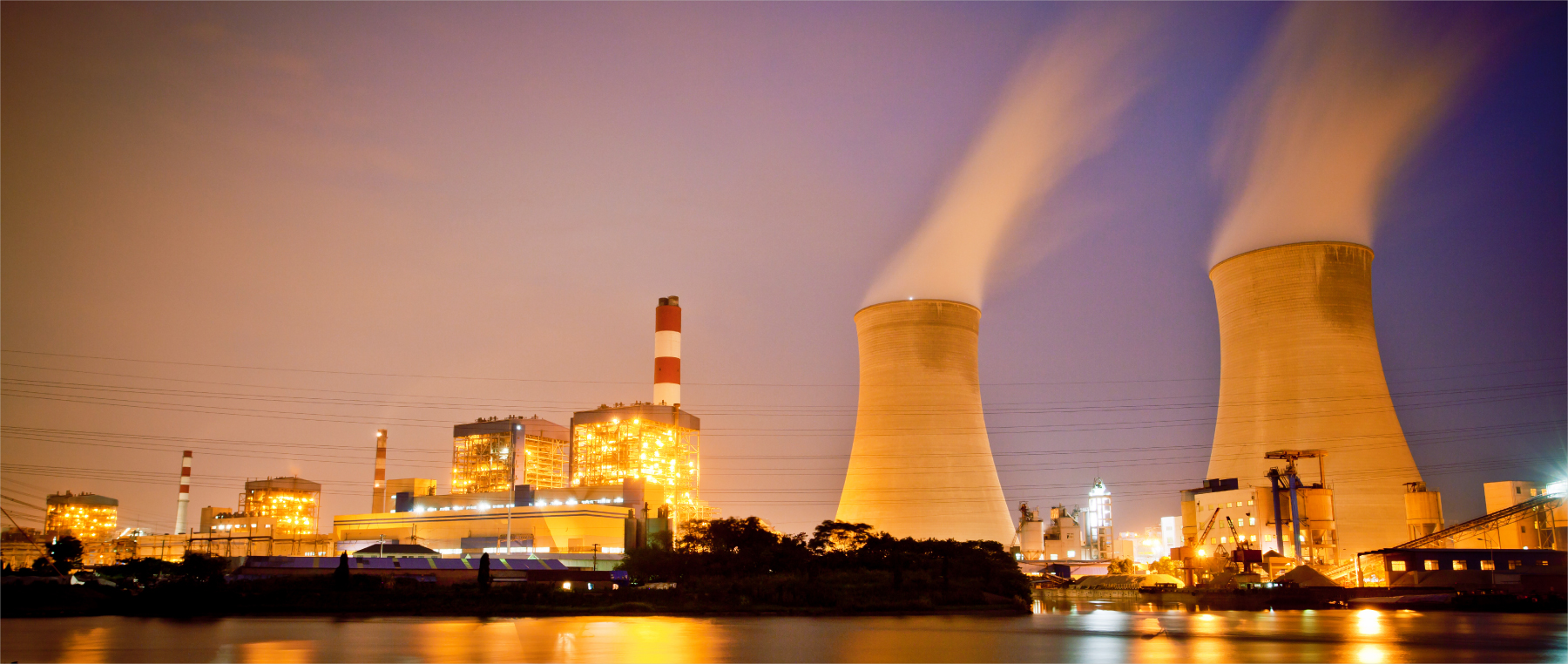
India is the world's third largest producer and consumer of electricity. And while renewable energy will take over a larger share of power generation in India, thermal power will continue to meet India’s base power needs for the foreseeable future. More than 65 percent of India's electricity generation capacity comes from thermal power plants, with 85 percent of the country's thermal power generation being coal-based.
Compressed air at a power plant finds application in coal handling, operating pneumatic instruments connected with boilers, turbines, generators, precipitators and ash handling system.
The air system in a thermal power plant is divided into instrument air and service air. As the name suggests, instrument air is used to operate pneumatic instruments where the quality of instrument air is of paramount importance; mandatorily in line with the ISO 8573 Class-1 norms, thereby ensuring pulsation-free discharge air. This air passes through the solenoid valves of various pneumatic controllers, resulting in precise control of valve operations.
Service air is required for the cleaning, purging of filters and for ash transportation. Though the service air quality requirements are not as stringent as those of instrument air, several thermal power plants use a single compressed air solution to address both the service air and instrument air needs, thereby easing the requirement of spares and related inventory.
Power plants are categorized based on capacity generation in megawatts. Traditional power plants generate capacity between 250 to 500 megawatts. With recent developments, the present power plants are designed to generate capacity up to 1200 megawatts. These power plants are termed as ultra-supercritical plants. With advancements in technology, these power plants occupy the same space as that of traditional power plants thereby resulting in space and utility savings together with operational cost conservation.
Over the years, technological advancements have led to the optimisation of operational costs across power plants in India. Oil-free screw air compressors and centrifugal air compressors have been strongly considered due to high reliability and low cost of operations, especially when compared with lubricated screw and reciprocating air compressors. Centrifugal air compressors have found adoption in applications that require huge volume of air beyond 3500Nm3/hr, thereby justifying the capital cost, and reducing the number of compressors required, while resulting in higher plant efficiencies.
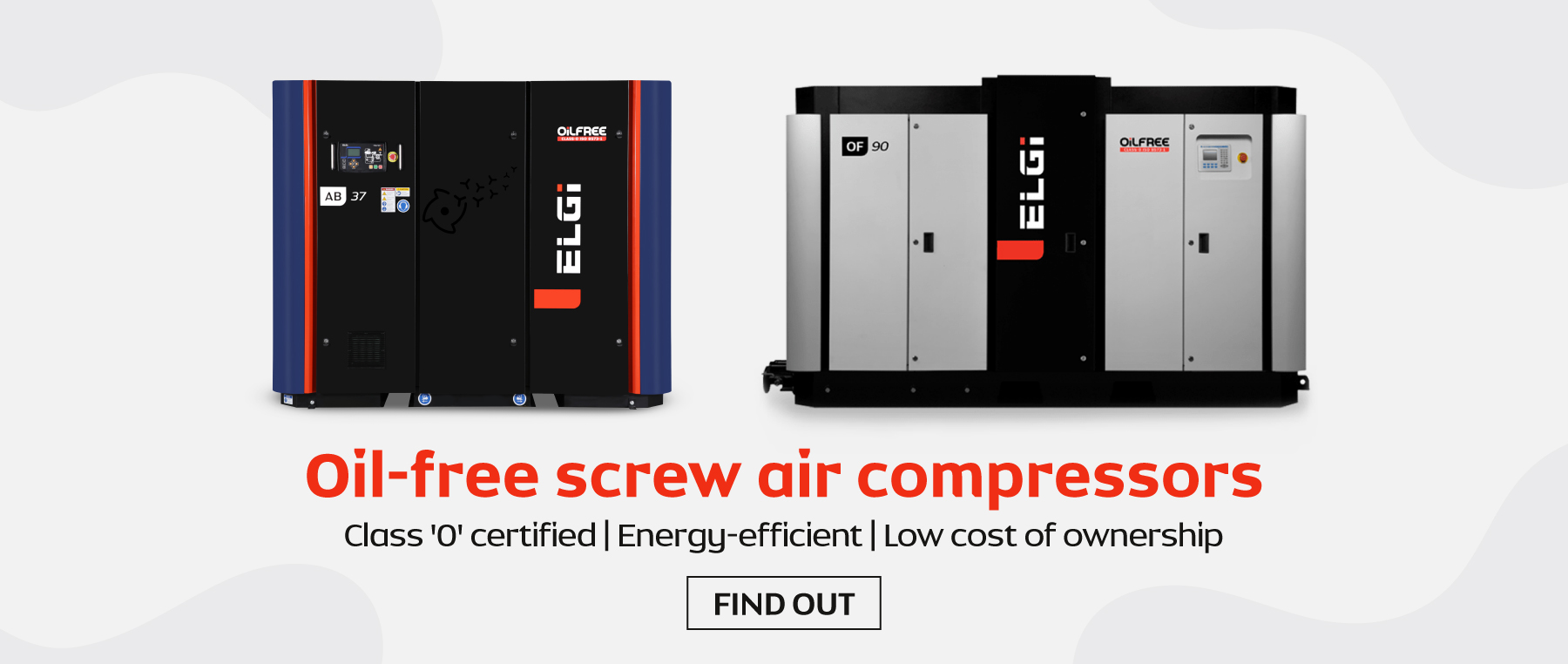
Oil-free screw compressors are the solution of choice for applications in which there is high fluctuation in loads. At high varying loads, these compressors are highly adaptive and ensure consistent pressure which is critical for the operation of pneumatic valves and actuators in the power plant. In addition, when compared with lubricated screw or reciprocating compressors, oil-free compressors ensure zero residual oil in the pipeline, thereby eliminating the risk of oil fumes and fire, and ensuring safety levels at the plant.
In case of a lubricated air compressor, power plants require standby machines while they conduct overhauls at frequent intervals. However, with oil-free technology, users can be assured of consistent performance, resulting in overhauls at 5-year intervals, significant capital cost savings and lower expenses for downstream oil filtration systems.
India’s expansion in industrial activity and growing urban and rural population will boost the demand for electricity, causing an expansion of thermal power plants and their capacities in the country. Oil-free compressed air technology will continue to witness strong adoption on account of lower operational costs and zero oil fumes, enabling power plants to lower their carbon footprint while paving the way for a greener environment.