Duty Cycle of Piston Compressors – Deciphered!
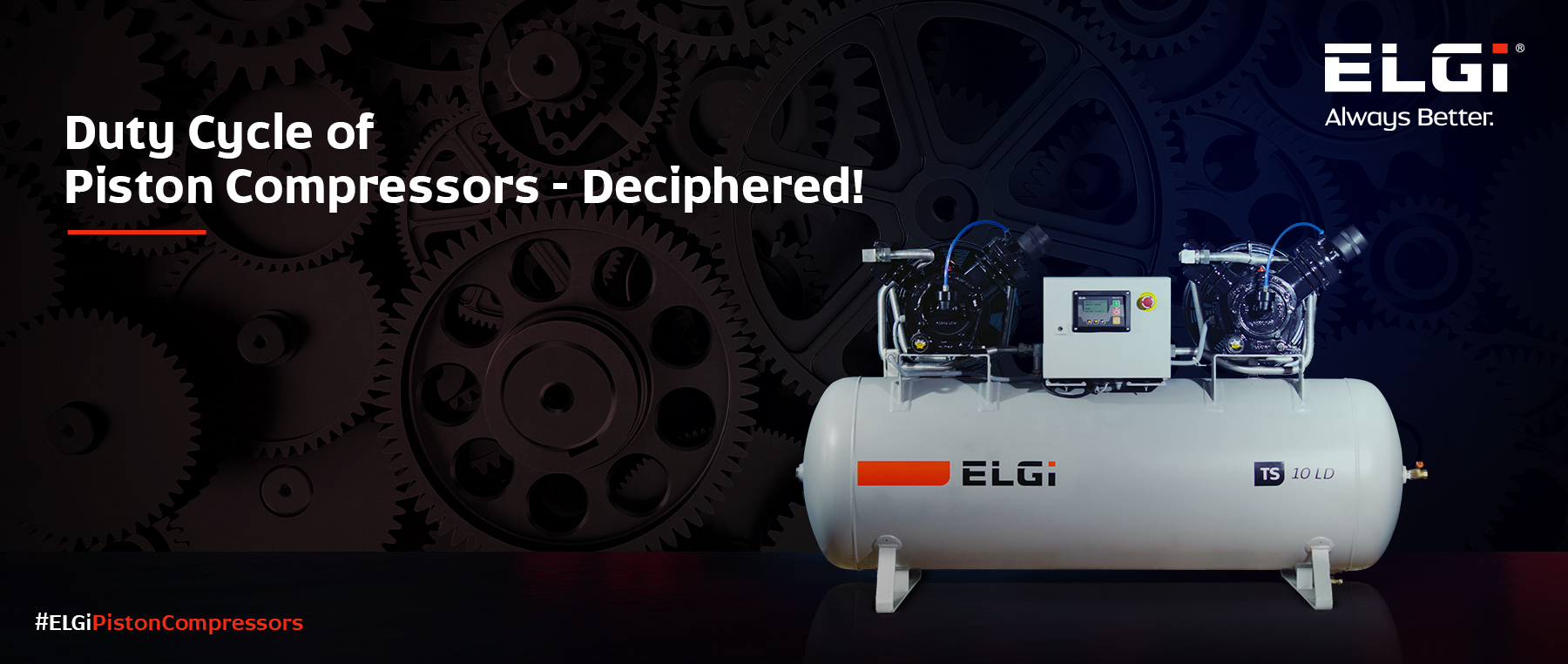
Selecting the right compressor for an application is highly critical. Apart from the quality of air, pressure and flow are the determining factors to choose the compressor technology (Piston, rotary, centrifugal, etc.) for any given application as each compressor technology has an optimal flow output for a set pressure.
Unlike rotary compressors that are designed to run continuously without wear or damage due to overheating, piston compressors cannot run continuously for extended periods as their design has a lot of moving parts, and the cooling and lubrication system is basic. Piston compressors thus have a specified percentage of time they can run without causing any sort of damage to the compressor.
What Is an Air Compressor Duty Cycle?
To understand the air compressor duty cycle it is important to first know what cycle time means. When it comes to piston compressors – they run on a start/ stop cycle; meaning when the desired maximum pressure is reached the compressor stops and starts back only when it reaches a set minimum level. The time between one stop and start is the total cycle time.
The duty cycle is generally represented as a percentage. It is the time duration a compressors’s top block runs to provide pressurized air at a defined flow rate relative to the compressor’s cycle time.
Why Is Duty Cycle Important?
The duty cycle is important as it helps to understand how efficiently a piston compressor functions by stopping and starting during use. It helps to determine if a given compressor model will fulfil the air needs of the application when sizing the compressor system.
It is also important for ensuring the optimum life of the compressor, as exceeding the recommended duty cycle can prematurely wear out or damage the internal components.
Duty Cycle Deciphered
If a piston compressor’s cycle time is 10 minutes, and it runs for 7 minutes during that time, then it runs on a 70% duty cycle, which means 3 out of 10 minutes the compressor will be resting/cooling down during a cycle.
A piston compressor that specifies a 100% duty cycle does not mean it can run continuously, but it can provide air at a specific pressure and flow for the time it runs (In the above- said case it is 7 minutes) with the help of a storage tank.
Why should Duty Cycle be optimum?
Heat is generated due to friction while the compressor is operating. Primary source, which is the friction between millions of air molecules while getting compressed makes compressed air very hot. The secondary source of friction are the moving parts inside the compressing unit, which raises the temperature of the cylinder as high as 150 to 200 Deg c.
99% of the industrial piston compressors come with a basic splash lubrication system –here the oil properties play a vital role in ensuring proper lubrication. Excess heat generation deteriorates the oil properties thereby impacting the lubrication.
The cooling system is not as sophisticated as what is available in other types of compressors. In a piston compressor, the cooling is majorly forced air cooled with fabricated or casted fan pulleys mounted on the compressor shaft and Copper or Aluminium pipes acting as coolers. These require non-operational time to ensure sufficient cooling time and avoid further heat generation between cycles.
Effects of running at 100% Duty Cycle
Some of the effects of running a piston compressor at 100% duty cycle are
- Piston seizure in the piston housing due to excessive heat in the cylinder
- Vales expand and jam with continuous exposure to a higher temperature, causing catastrophic failure of the compressor
- Changes in oil properties lead to higher oil carryover
- Continuous exposure to higher temperatures leads to higher condensate formation in the receiver tank thereby increasing moisture carryover to the downstream equipment and to the end equipment
- Higher maintenance cost due to quicker wear and tear of internal parts
Recommended Duty Cycle
It is critical to know that the 100% duty cycle on a piston compressor does not mean that it can run continuously. Doing so can damage the compressor, resulting in premature wear and higher maintenance costs.
Different brands recommend different duty cycles based on their design standards. The ideal duty cycle recommended for piston compressors by ELGi is a 70:30 duty cycle.
Always choose a compressor that best suits the application requirement!