Common Signs of Air Compressor Wear and Tear: When to Perform Maintenance
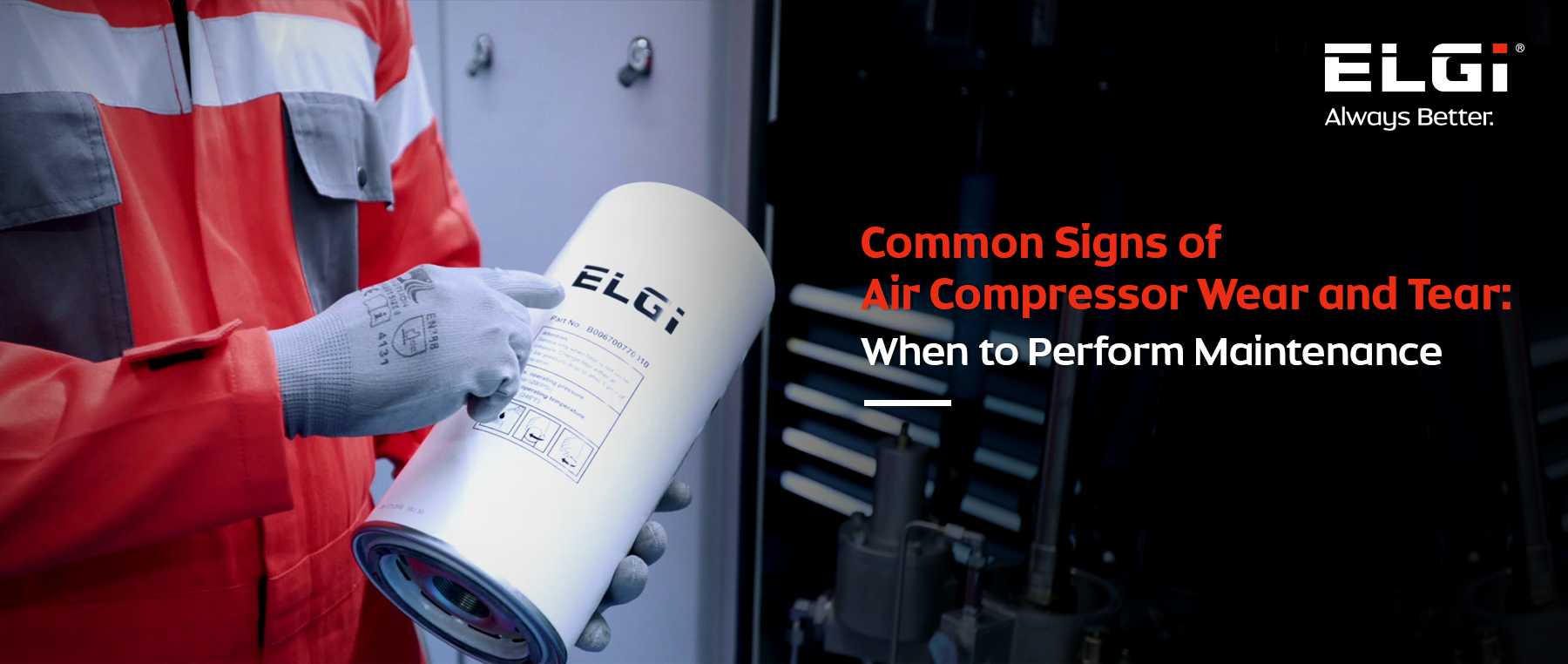
Maintenance plays a vital role in the effective and efficient running of a compressor. If you don’t service the compressor at the specified intervals, the components will wear and tear quickly, leading to unexpected breakdowns.
Here we will look at the common indications of wear and tear in an air compressor that should not be neglected. If you notice any of these in your compressor, maintenance is in order.
- Air leak: Worn-out or damaged hoses, joints, connectors, or fittings are the root cause of air leaks. Arresting the air leakages then and there will ensure the compressor works efficiently and that energy is saved.
- Low outlet air pressure: If the compressor's output pressure is lower than usual, the internal parts may get worn-out or damaged. Operating a compressor in such a condition can prove hazardous.
- Reduction in airflow: When rotors and seals are worn out, there is a reduction in the airflow of a compressor. Running the compressor continuously without identifying the root cause can lead to a major breakdown.
- Warning alerts: The controller continuously monitors the compressor’s parameters and shares updates/ alerts in case of any deviation. These alerts should not be ignored, and immediate action must be taken to avoid major failures.
- Decreased efficiency: Wear and tear in the compressor directly hampers its efficiency. If you happen to notice a drop in the efficiency, examine your compressor components closely.
- Excess power consumption: The compressor will consume excess power if the valve kits are worn out, or the filter and separator element face obstruction. Adhere to the maintenance schedule and replace the parts on time to avoid excess power consumption.
- Drop in oil Pressure: If there is a drop in oil pressure, do not ignore it. This may indicate issues with the filter or damaged internal components.
- Abnormal noise: An unusual sound that is not associated with the compressor system could be a sign of damaged or worn-out parts. When you notice such a sound from your compressor, shut it down immediately. Then, get it checked thoroughly to identify the cause.
- Overheating: Compressors are designed to run at specific temperatures. Excessive friction of internal components, improper lubricants, or low lubricant levels increase the running temperature of the compressor. Operating the compressor at a higher temperature will cause damage to the rubber components, seals, and gaskets.
- Oil Contamination: When the internal components undergo wear and tear, the metallic particles may get mixed with compressor oil. This will lead to a complete system failure. That is why you must check the quality of the oil at regular intervals as recommended and change the oil if required.
- Frequent tripping: If the compressor trips frequently, it’s a warning that a part of the system malfunctioning. This may be due to the gradual deterioration of components.
- Excess vibration: Excess vibration is an indication of improper mounting or misalignments. This should be repaired immediately to avoid further wear and tear.
.
- Oil carryover: Oil can contaminate compressed air systems when there is an issue with the oil separator. When oil carried over the air gets contaminated, it causes damage to the downstream equipment.
Therefore, to ensure optimum efficiency, a compressor should be continuously monitored. Maintain a logbook and keep track of when a replacement or service is due.
In a nutshell, one must always use genuine spare parts and adhere to the service schedules to achieve the desired longevity of the components. Any wear and tear should be given immediate attention to prevent major breakdowns.
As most of the system failures happen due to lack of maintenance, this is a crucial step to ensure the compressor continues to work efficiently.